Last Updated: October 20, 2023
A container surveyor will inspect your containers’ condition. So, it’s important that you check your boxes too. Why? Read this blog to learn how container inspection can save you from delays and disputes.
In this blog, you’ll learn:
- Role and responsibilities of a container surveyor.
- Why different shipping players should get containers surveyed.
- Four major types of container surveys: on-hire, off-hire, CSC inspections, condition survey, and survey of new containers.
- The 7-point checklist container surveyors follow.
- How to find both containers and surveyors in one dashboard.
Shipping containers are essential to global trade. From food-grade products to heavy machinery, you can pack, store, and ship anything across the globe. Naturally, for such safe and seamless transportation, you’ll have to ensure that your containers are in good condition.
Your container’s condition will determine the safe and secure transportation of your cargo. So, how can you check if your containers are cargo-worthy? Fortunately, you can rely on container surveyors to do that for you.
On xChange, you can easily find both containers and container surveyors. You can lease, buy, and sell equipment on our online container marketplace. In fact, you can also ask for a container survey to ensure you’ve got the right box.
We have a network of container surveyors in 4,000 depots across the world. Want to find a qualified surveyor at your location? Click on the banner below to talk to our experts.
Who’s a container surveyor?
A container surveyor is an authorized and licensed individual who inspects, surveys, and examines container equipment. They’ll check your container’s structural condition and integrity. This is to confirm if they’re qualified to store or carry your cargo on the rough seas.
Usually, you’ll need a container surveyor before or after you lease or buy a container. Let’s look at an example to understand container surveying better.
You’re leasing a container to import food items from China to Belgium. Obviously, you want your cargo to pass the food inspections by Belgian customs. So, you ensure that the container is suitable to carry food items in the first place. Do this before you sign the deal with the lessor.
After inspecting the equipment, the surveyor will issue a container survey report. This document certifies whether the box is suitable for the purpose of its leasing.
Some customs authorities charge a container inspection fee. A container inspection fee is a charge imposed on shipping containers to cover the costs associated with inspecting and ensuring compliance with various regulations and standards. Container inspection fees can vary widely depending on the country and the nature of the inspection.
They may be a fixed fee per container or calculated based on the type of goods, the level of risk associated with the shipment, or other factors. Importers or exporters are usually responsible for covering these fees, and they are considered part of the overall cost of international trade.
Now, let’s look at other instances in which you’ll need a container surveyor.
Who needs a container survey report?
Any organization using containers to ship cargo can recruit container surveyors. These include container owners, lessors, lessees, buyers, sellers, shippers, and even freight forwarders.
And you can use the container survey report to prevent conflicts. In fact we’d suggest you to use the container survey report to safeguard yourself from claims of container damage.
If you’re a container leasing company or a lessor, you’ll do a survey to record the condition of your box before and after leasing. And in case your box got damaged during the transportation, you can use the container survey report to seek repair measures.
On the other hand, if you’re a buyer or lessee of SOC containers, the survey will determine whether the containers meet the criteria you had requested. After all, you should get what you pay for. And a container survey will confirm this for you.
On xChange, you can not only deal with containers but also get them surveyed at a nominal price. Instead of searching container surveyors on their own, our members can simply click the ‘Request Survey’ button to get the ball rolling!
And yes, it’s actually as easy as it sounds. We have a network of qualified and licensed container surveyors. On your command, our surveyors will contact your depot and start arranging the container inspection.
Want to have a closer look at how you can lease, buy, or sell containers? And also book surveys? Click on the banner below to see it for yourself.
Types of container surveys
So now you know what container surveys and their uses are. But did you know that there are different types of these surveys too? Let’s learn which one suits you the best.
On-hire survey
On-hire survey is the most common survey for one-way leasing moves. In this case, a surveyor inspects the containers before leasing. This is done to make sure that the containers meet the conditions the lessor and lessee had agreed upon.
Your container survey report will include a detailed record of any pre-existing damages or other defects of the container. You must be wondering if booking an on-hire survey is necessary?
As a lessee, ensure that your containers are inspected prior to booking. The container survey report will guard you against any damage that occurred before delivery of the container. To put it simply, it helps you avoid conflicts.
However, the most essential reason for conducting on-hire surveys is to confirm if your container is suitable to carry the specific cargo. For example, you can carry only food items in a food-grade container. Similarly, you can carry only chemicals in chemical-grade containers, and so on.
Therefore, the container surveyor will inspect the box and classify it as general cargo, food-grade, or other standards as specified by you.
For special containers such as reefers, an inspection would also include a check of reefer machinery, testing motors for bearing noise, and leakage. To know more about reefer container inspection and repair, click here.
We provide an on-hire survey to our members. Interested in booking one today? Click on the button to get started.
Off-hire survey
An off-hire survey is conducted at the lessor’s end after you return the container. This is done to check if any damage you cause is within the agreed leasing terms.
The container surveyor will document the results, including a breakdown of all adjustments and repairs. After that, the surveyor will propose economical repair methods. You can also verify if the repair costs are in line with the local market from the container survey report.
Want to book an off-hire survey for your boxes? Get the best estimate on damage and repair costs by clicking on the button below.
CSC inspection
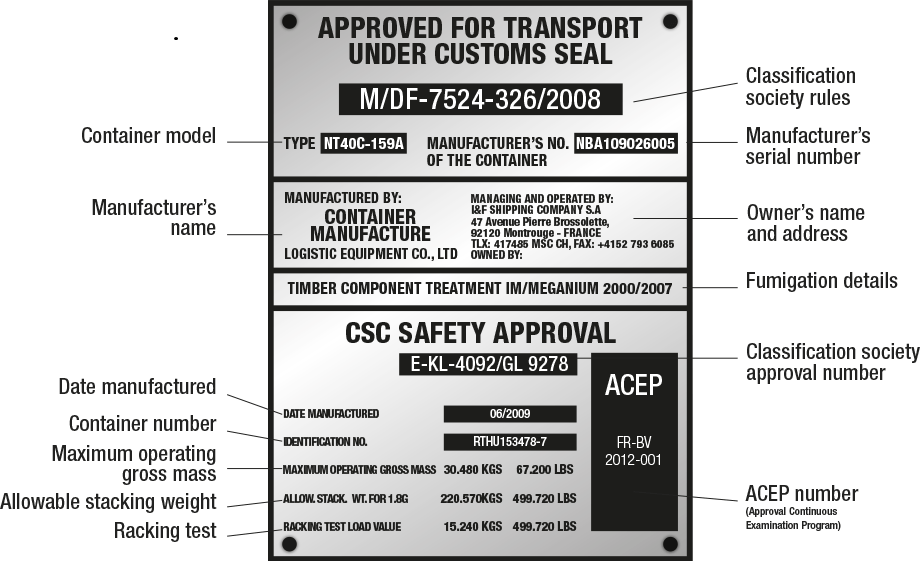
Infographic is a courtesy of the BIC – Bureau International des Containers
Every container used for international cargo transport must have a valid CSC plate. You’ll need a CSC inspection for containers if the CSC plate is invalid or expired. It’s hands-down the most important survey type. Only a valid CSC plate will allow your boxes to enter a terminal, and even to get loaded on vessels.
You can get a CSC inspection certificate made directly by our surveying partners. Just click on the button to book a CSC inspection for your containers.
Condition survey
A condition survey is typically used to verify whether the condition of the container is up to a specified standard. The container surveyor will record the condition of the container, including any damages or faults. If the condition isn’t suitable for use, they’ll propose a cost-effective next step. You might’ve to repair the container, return it to the lessor, or even scrap it.
If you’re a member of xChange, you can easily book a container with just a few clicks. Why waste time looking for a container surveyor, when you can recruit an expert by clicking on a button? Try it for yourself!
Survey of new containers
As the name suggests, this survey is done on new containers. You’ll find these surveys carried out at the container manufacturing site. The purpose is to make sure that these newly-built boxes follow the standards set by the ISO (International Organization for Standardization).
So far, we’ve seen different types of container surveys. And now you must be curious how exactly these surveys are carried out. Well, let’s see that in the next section.
7-point inspection checklist for the container survey report
A surveyor issues you the container survey report after thoroughly inspecting your container. To do so, surveyors rely on a 7-point checklist. Let’s give you a sneak peek of a container surveyor’s cheat sheet.
Outside / Undercarriage
- Inspect prior to entering the facility.
- Support beams on the undercarriage should be visible.
Inside / Outside doors
- Make sure secure and reliable locking mechanisms are used.
- Look for different color bonding materials.
- Check for any loose bolts.
- Be on the lookout for plates and repairs.
Right side
- Check for any unusual repairs to structural beams.
- Repairs to walls on the inside of the container must be visible on the outside.
- Use tools to tap sidewalls. Listen and feel for hollow sounds.
Left side
- Check for any unusual repairs to structural beams.
- Repairs to walls on the inside of the container must be visible on the outside.
- Use tools to tap sidewalls. Listen and feel for hollow sounds.
Front wall
- Make sure that the blocks and vents are visible.
- Use tools to tap the front wall. Listen and feel for hollow sounds.
- Use a rangefinder, measuring tape, or even a string to measure the length of the container.
Ceiling / Roof
- Make sure the height of the ceiling is accurate. Blocks and vents should be visible.
- Repairs to the ceiling on the inside of the container should be visible on the outside.
- Use tools to tap the ceiling. Listen and feel for hollow sounds.
- See if you’re uncomfortable inside the container. If yes, the height of the interior ceiling may be incorrect.
Floor (inside)
- Make sure the floor is the correct height from the ceiling.
- Check if the floor is flat. You don’t need to step up to get inside.
- Make sure the floor has a uniform height.
- Be on the lookout for any unusual repairs.
Container loading checklist
A container loading checklist is a document used to ensure that the loading process of goods into shipping containers is carried out systematically and in compliance with safety and regulatory standards. The checklist helps to minimize the risk of damage to goods during transit and ensures that the container is loaded efficiently. This document is important to have during the inspection process. You might find the following on a standard container loading checklist:
- Verification of shipping documentation
- Inspection of container for structural integrity and cleanliness
- Confirmation of weight distribution within permissible limits
- Use of appropriate packing materials and securing mechanisms
- Proper labeling of items with relevant instructions
- Cross-checking contents against the packing list
- Sealing the container with authorized seals
- Adherence to a loading plan for efficient space utilization
With great checklists comes a great responsibility. There are a couple of them that container surveyors must carry out and maintain. Let’s discuss:
Responsibilities of a container surveyor
The checklist would’ve given you an idea of how important a container surveyor’s role is. However, the surveyor isn’t responsible for only following a checklist.
There’s a range of responsibilities that a surveyor has to perform. Here they are:
- Surveying the shipping containers of the organization that hired them. The organization may even ask to survey the containers they’re planning to acquire.
- Surveying the damages and condition of the container. And recommend repairs accordingly.
- Reporting on the cleanliness of containers.
- Ensuring the presence of the required markings on the container.
- Conducting routine checks during the stuffing and destuffing of the container.
- Keeping appropriate records of loading, unloading, closing, and sealing of the container.
- Keeping a track of inspections.
- Helping the organization improve the management of their freight containers.
- Collaborating and coordinating with logistics staff on container management.
Find a qualified container surveyor with xChange
If you’ve been in the shipping industry for long, you’d know how rare securing containers within your budget is . You’ll spend the majority of your time making endless calls to just get quotations. And repeating the process to recruit a container surveyor would obviously be tedious.
What if we tell you that you can easily break away from this cycle? Because you really can! On our online marketplace for containers, you can lease, buy, or sell containers in 2,500+ locations within minutes. Just state your requirement and get offers in one dashboard. Select the one that suits you the best and negotiate to sign the deal.
And while you’re at it, also book container surveys in a matter of seconds. Once you finalize your deal, just click on the ‘Request Survey’ button on the dashboard to book a survey. Don’t worry, we’ve got a strong network of licensed container surveyors in almost 4,000 depots globally. And did we tell you that our rates are very nominal?
Talk to our experts to learn what the charges for different types of container surveys at your location are. Click on the banner to schedule your call today!
What is a container surveyor?
A container surveyor is an authorized and licensed individual who inspects, surveys, and examines container equipment. They’ll check container’s structural condition and integrity to confirm if they’re qualified to store or carry cargo on the rough seas.
What is container survey report?
A container surveyor issues a container survey report after inspecting the equipment. This report summarizes the container's condition and certifies whether the box is suitable for the purpose of its leasing.
What is container inspection?
A container inspection checks whether the condition of the container is suitable to carry or store cargo. The inspector or the surveyor will check whether all the terms of ISO intermodal transportation are met by the container.